STMicroelectronics optimise sa production de froid
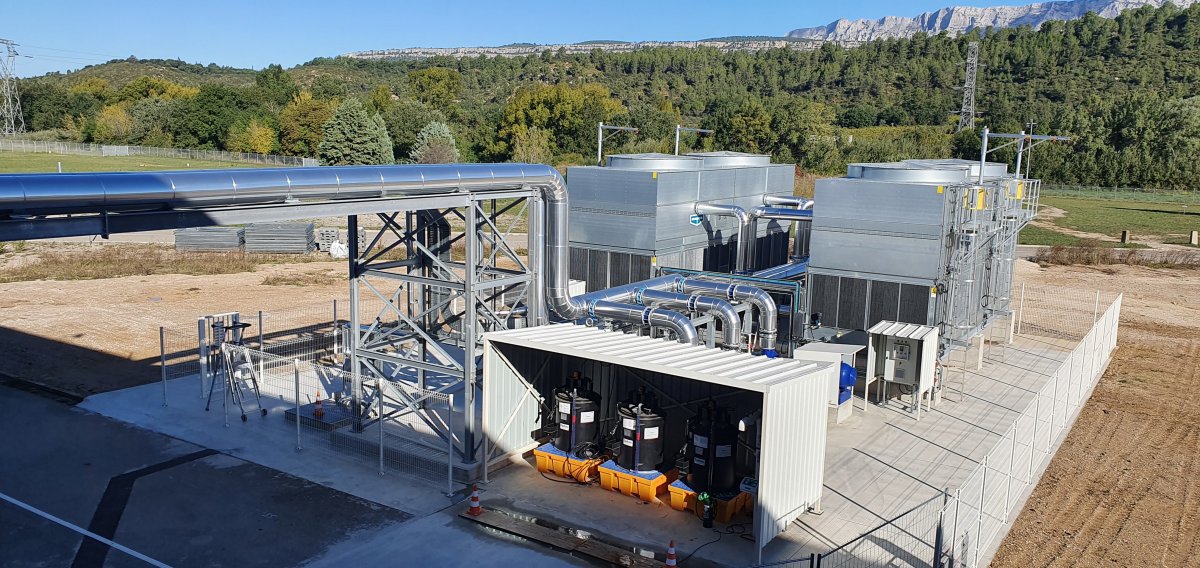
Dalkia a modifié le procédé de fourniture de froid d’une usine de STMicroelectronics dans les Bouches-du-Rhône. Effectuée dans des conditions draconiennes, cette opération doit générer 20 % d’économies d’énergie.
Comment intervenir sur un procédé industriel, pour en améliorer la performance énergétique, s’il ne cesse jamais de fonctionner ? C’est le défi auquel a été confronté Dalkia sur un site de STMicroelectronics au Rousset (voir photo), dans les Bouches-du-Rhône. Après dix-huit mois d’études et de travaux, une nouvelle installation de fourniture de froid y fonctionne depuis la fin 2021. Officiellement inaugurée en juin dernier, elle doit réduire la consommation d’énergie de 20 % par rapport à la précédente. Bien que classiques, les nouveaux équipements ont été déployés dans le cadre très précautionneux de l’industrie électronique. Le site du Rousset est en effet l’une des quatorze usines de STMicroelectronics. D’une superficie de 37 hectares, il compte 2 800 personnes, dont la moitié pour la fabrication de composants électroniques.
La spécificité de l’usine tient surtout à ses conditions de production. Des plaquettes de silicium de 20 centimètres de diamètre – environ 10 000 par semaine – y sont fabriquées en respectant des critères très stricts, par exemple en termes d’hygrométrie. Ou encore de poussières : les 600 équipements, répartis dans les 10 000 mètres carrés de salles blanches, doivent opérer dans « un environnement cent fois plus propre qu’un bloc opératoire », compare STMicroelectronics.
Autre particularité : l’usine fonctionne 365 jours par an et 24 heures sur 24. L’industriel, qui revendique déjà une baisse de 50 % en quinze ans de l’énergie consommée par unité produite, voulait la réduire également pour la production de froid. Celle-ci était jusqu’alors assurée par des “chillers”, des groupes de production de froid dont la chaleur extraite sert à réchauffer les bureaux du site. Pour les remplacer, l’enjeu consistait, non seulement à identifier la bonne solution technique, mais surtout à réaliser la substitution dans les salles blanches sans arrêter la production.
Système d’aerofreecooling
Pour y parvenir, « trois solutions ont été déployées », présente David Campredon, responsable travaux du centre opérationnel industrie Provence-Alpes-Côte d’Azur de Dalkia. Premièrement, Dalkia a installé un système d’aerofreecooling d’une puissance thermique de 6 MW. Il utilise l’air extérieur – via deux tours de refroidissement – pour baisser la température d’une boucle d’eau. Auparavant, cette boucle était refroidie à 18°C par les groupes frigorifiques. La substitution par les tours de refroidissement génère une première baisse de la consommation d’électricité de 3 GWh/an. Des groupes froids ont tout de même été conservés pour assurer la continuité de la production en cas de défaillance de l’aerofreecooling.
Les nouveaux équipements possèdent des puissances équivalentes aux précédents modèles. En l’occurrence, ces cinq machines représentent des puissances de 5,6 MW pour deux d’entre elles et 2 MW pour les trois autres. Mais elles sont plus efficaces, ce qui permet une diminution supplémentaire de la consommation de 1,5 GWh/an. Au passage, des fluides HFO ont été choisis comme frigorigènes dans les nouvelles machines, pour leur plus faible potentiel de réchauffement global vis-à-vis des émissions de gaz à effet de serre.
Enfin, un système de régulation numérique a été mis en place. Il optimisera le fonctionnement de l’ensemble des équipements : l’aerofreecooling, les nouveaux groupes froid et surtout le passage de l’un à l’autre de ces systèmes. L’aerofreecooling sera utilisé en priorité. Mais sa principale limite de fonctionnement étant la température extérieure, « il peut fonctionner neuf mois dans l’année », précise David Campredon. Le reste du temps – l’été – ou bien en cas de défaillance, les groupes froid prennent le relais. Le dispositif de régulation sert à anticiper leur démarrage ou mise à l’arrêt en fonction des conditions atmosphériques et des besoins de production. Le passage d’un système à l’autre se fait automatiquement.
Maquette 3D
Au total, les économies d’énergie atteignent donc 4,5 GWh, qui représentent un gain de 20 %. STMicroelectronics ne communique pas sur le montant de l’investissement. L’industriel indique simplement qu’une partie a été prise en charge par les certificats d’économies d’énergie (CEE). EDF, maison-mère de Dalkia, s’est occupé du volet CEE du projet. « Les équipements que nous avons installés sont finalement assez classiques, c’est le chantier qui était hors-norme », témoigne David Campredon, « puisque la production ne pouvait pas être arrêtée, nous avons réalisé une maquette 3D de la ligne de fabrication ».
Cette maquette a permis de repérer la possibilité de raccorder l’aerofreecooling au réseau de froid déjà en place. « Elle nous a aussi fait constater que nous ne pouvions pas rentrer les équipements, en particulier les tours de refroidissement, dans la zone de production sans les démonter au préalable, puis les remonter à l’intérieur ». Ces conditions de chantier expliquent en grande partie le délai de 18 mois d’études et d’installations. « Pour que STMicroelectronics puisse conserver sa puissance maximum, nous avons cadencé le raccordement de chaque nouveau groupe froid ». Ils ont été changés un à un, en utilisant à chaque fois un groupe de location pour assurer la continuité du fonctionnement.