Comment les cimentiers tentent de se bâtir un avenir décarboné ?
Pour atteindre la neutralité carbone à l’horizon 2050, l’industrie cimentière française mise sur des leviers traditionnels – optimisation des procédés, combustibles alternatifs et substituts au clinker – mais ne pourra pas faire l’économie d’investir dans de coûteux systèmes de capture du carbone.
Heidelberg Materials devrait expédier en 2025 les premières tonnes de dioxyde de carbone captées sur sa cimenterie de Brevik en Norvège. Elles sont destinées à être stockées dans des aquifères salins en mer du Nord. Ce premier terminal CO2 au monde, construit par la société Northern Lights (Equinor, Shell et TotalEnergies), préfigure une des solutions envisagées par les cimentiers, à l’instar d’autres industriels, pour s’approcher de la neutralité carbone à l’horizon 2050. La route est encore longue, mais les enjeux sont colossaux.
Parmi les matériaux de construction les plus utilisés dans le monde, le ciment Portland* est à l’origine de 6 à 8 % des émissions de CO2 planétaires. « S’il ne représente que 12 % de la composition d’un béton, le ciment pèse 85 % de son empreinte carbone », rappelle Bruno Paul-Dauphin, directeur des solutions béton bas carbone chez Vinci Construction.
Dans ce contexte, la pression règlementaire est montée d’un cran ces dernières années, en France comme en Europe. Le système européen d’échange de quotas d’émission (SEQE-UE) va accélérer à partir de 2026 la diminution des quotas gratuits alloués aux cimentiers, avec une disparition totale attendue en 2034. Dans l’Hexagone, la réglementation environnementale (RE2020), qui régit la construction neuve, fixera quant à elle de nouveaux seuils en matière d’empreinte carbone au 1er janvier 2025. Enfin, la trajectoire de décarbonation établie par le Gouvernement pour les cinquante sites les plus émetteurs de gaz à effet de serre (GES) hexagonaux mobilise également la filière : sur les vingt-cinq cimenteries françaises, vingt figurent sur la liste établie en novembre 2022.
Leviers traditionnels
La marche à franchir est haute pour les cinq cimentiers opérant dans l’Hexagone : Eqiom (groupe CRH), Heidelberg, Imerys, Lafarge (groupe Holcim) et Vicat. Ces poids lourds anticipent un plan d’investissement cumulé de plus de cinq milliards d’euros d’ici 2040 en vue de se décarboner. Des financements publics accompagnent leurs ambitions notamment dans la capture, la valorisation et la séquestration de carbone (CCUS), principalement le Fonds européen d’investissement (FEI) et l’appel à manifestation d’intérêt lancé par le Gouvernement français en avril 2024.
La capture du CO2 est cependant loin d’être la seule voie explorée par les acteurs du secteur. France Ciment, l’organisation représentative de l’industrie cimentière, a fait ses calculs dans sa nouvelle feuille de route de décarbonation publiée en mai 2023. Pour abaisser de moitié les émissions de la filière à l’horizon 2030 par rapport à 2015, elle mise pour 23 % sur le captage de CO2, et pour 27 % sur les leviers « traditionnels ». Ceux-ci comprennent l’optimisation des procédés, l’emploi de combustibles de substitution, la réduction de la part de clinker dans les ciments, etc. Par conséquent, les émissions décroîtraient à 4,8 millions de tonnes équivalent CO2 par an, contre 10,4 Mt CO2/an en 2015.
Ces leviers traditionnels sont connus. En effet, « les cimentiers ont toujours commercialisé des gammes à moindre impact environnemental qui étaient utilisées pour des raisons techniques et économiques plutôt que pour leur empreinte carbone réduite. En quelques années, la tendance s’est inversée avec une forte demande de bétons bas carbone », poursuit Bruno Paul-Dauphin.
Vinci mise sur les bétons d’ingénierie
Plutôt que d’acheter des ciments décarbonés, Vinci Construction recompose lui-même la recette de ses bétons directement dans les malaxeurs des centrales à béton partenaires, abaissant ainsi la part de ciment. Couramment utilisée, cette technique de « bétons d’ingénierie » a fait l’objet d’une mise à jour de la norme béton en octobre 2022. En lançant sa démarche baptisée Exegy, Vinci Construction veut massifier les bétons bas carbone sur ses chantiers en travaillant à la fois sur leurs formules, les méthodes et le matériel de chantier. Anticipant la réduction des ressources en laitiers de hauts-fourneaux, le major de la construction a conçu une solution baptisée Exegy L+C3 permettant de substituer le ciment par du filler calcaire (50 %) et des ultrafines comme les métakaolins (15 %), diminuant de 30 à 40 % la part de clinker. Ces bétons performanciels, formulés sur la base d’une étude préliminaire en laboratoire, ont notamment été utilisés en 2024 pour la réalisation des voussoirs d’un tunnel passant sous le canal du Midi dans le cadre de la connexion de la ligne B du métro de Toulouse.
Combustibles alternatifs
Pour bien comprendre les moyens d’action environnementaux, il faut se plonger dans le procédé de fabrication du clinker, le constituant actif du ciment. C’est le principal responsable des émissions de la filière. Celui-ci est obtenu par cuisson à haute température d’un mélange de calcaire et d’argile, une opération qui pèse pour un tiers des émissions de CO2. La réaction chimique qui s’en suit, la décarbonatation du calcaire (CaCO3) en chaux (CaO) et en CO2, est à l’origine des deux autres tiers des émissions. La cuisson à 1 450 °C nécessaire à la production de clinker a été historiquement obtenue par combustion de charbon et autres cokes de pétrole.
Par souci d’économie, les acteurs européens y ajoutaient déjà des huiles usagées, des farines animales, des pneus déchiquetés, des résidus de bois, etc. « Les installations existantes peuvent intégrer de l’ordre de 10 à 20 % de combustibles de substitution, mais aller au-delà de ce seuil implique des modifications conséquentes », détaille Alain Cordonnier, président de Fives FCB (Groupe Fives).
Au Sénégal, ce concepteur de lignes de production de ciment mettra en service début 2025 une ligne fonctionnant à 70 % avec de la biomasse locale, en l’occurrence des cosses de cacahuètes.
Poids carbone du clinker
Toujours pour des raisons financières, les cimentiers ont utilisé des substituts au clinker : des laitiers de hauts-fourneaux (sous-produits métallurgiques), des cendres volantes (particules des centrales électriques au charbon), des pouzzolanes (roches volcaniques), etc. Si le CEM I ou ciment Portland contient au moins 95 % de clinker, le CEM II comporte jusqu’à 35 % d’autres constituants (laitiers, fumées de silice, cendres volantes, etc.). Le CEM III contient entre 36 et 80 % de laitier de haut-fourneau, tandis que le CEM IV est un ciment à base de pouzzolane. Enfin, le CEM V ou « ciment pouzzolanique au laitier » contient 18 à 49 % de laitiers de hauts-fourneaux et de 18 à 49 % de cendres volantes siliceuses.
« Les produits alternatifs issus de la sidérurgie ou des centrales thermiques au charbon sont employés en Europe en substitut au clinker, mais les ressources disponibles décroissent. C’est pourquoi en France, les cimentiers ciblent davantage les argiles ou les calcaires broyés finement (fillers calcaires), des matières naturelles très présentes dans notre environnement », éclaire Éric Bourdon, directeur général adjoint du Groupe Vicat, en charge des performances et des investissements. France Ciment attend beaucoup de ces solutions pour abaisser le taux de clinker dans le ciment de 75 % en 2021 à 68 % en 2030 et 62,5 % en 2050.
Le Laboratoire des solides irradiés – unité mixte de recherche du Commissariat à l’énergie atomique et aux énergies alternatives (CEA), du Centre national de la recherche scientifique (CNRS) et de l’École polytechnique de Paris – a d’ailleurs publié une étude cette année en collaboration avec l’industrie cimentière. Elle caractérise une grande quantité de matériaux de substitution déjà utilisés ou candidats à l’être. Le verre recyclé serait un bon prétendant tout comme le biochar, un résidu issu de la fabrication du charbon de bois déjà employé comme substitut par Vicat. Mais ces solutions demeurent des solutions de niche à l’inverse des argiles et fillers calcaires, disponibles en quantité sur tout le territoire.
Parmi les autres leviers traditionnels susceptibles d’être activés, la modernisation des ateliers de broyage et de séparation du clinker figure en bonne position. Vicat a investi dans un nouveau séparateur sur son usine de Xeuilley (Meurthe-et-Moselle) afin de diminuer son ratio de clinker dans le ciment. « Le ciment est une colle préparée par broyage de clinker, gypse et calcaire. Si cette colle est mieux préparée, nous aurons besoin de quantités moindres de clinker. En étant plus méthodique dans les opérations de broyage, nous pourrons réduire de 3 à 5 % la quantité de clinker dans le ciment et donc d’autant les émissions de CO2 associées. Il s’agit d’investissements relativement modestes (de 5 à 7 millions d’euros) au regard des gains en CO2 potentiel », note Alain Cordonnier. Un nouveau séparateur sera également mis en service en 2025 par Eqiom sur sa cimenterie d’Héming, en Moselle.
Selon Fives FCB, la modernisation des ateliers de broyage, l’utilisation d’argiles calcinées et l’emploi de combustibles alternatifs abaisseraient au final de 40 % les émissions de CO2 du ciment. Faudra-t-il aller jusqu’au remplacement pur et simple des anciens ateliers de broyage pour maximiser les gains ? Le cimentier Vicat reste prudent, Éric Bourdon rappelant que « changer la totalité d’un atelier de broyage n’est pas anodin. C’est un billet de 30 à 50 M€. Nous le faisons dans le cadre de l’augmentation de capacité d’un site, ce qui permet d’amortir l’investissement. Cela a également été le cas il y a une quinzaine d’années dans notre usine amirale de Montalieu-Vercieu (Isère) ».
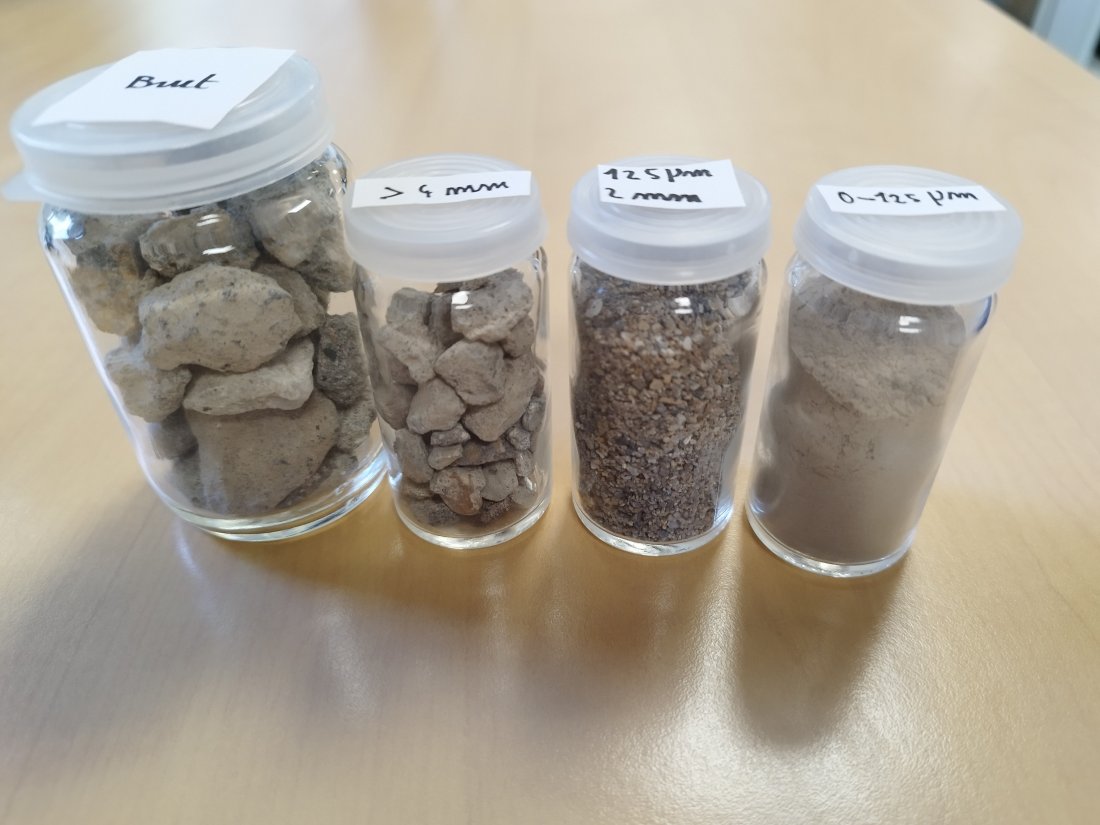
Les chantiers s’adaptent
Sur les chantiers de construction, les acteurs reconnaissent l’importance de remplacer en premier lieu – lorsque c’est possible – le béton par des produits biosourcés. La mise en œuvre d’une structure en bois couplée à des panneaux muraux en bois réduit considérablement le poids propre d’un immeuble, donc l’importance des fondations en béton nécessaires à la reprise de cette charge.
Pour Laure Hélard, la déléguée générale de France Ciment, l’objectif consiste à « faire mieux avec moins, en mettant moins de béton dans la construction, moins de ciment dans le béton et moins de clinker dans le ciment ». Demeure la question de la mise en œuvre de ces nouveaux bétons bas carbone (baisse de 30 % des émissions de CO2 par rapport à un CEM I), très bas carbone (baisse de 30 à 50 %) et ultra bas carbone (plus de 50 %). « Le clinker a le défaut d’être très émissif en GES, mais il offre une prise rapide, un atout pour conserver les cadences d’avancement d’un chantier. Les bétons bas carbone sont moins réactifs : leur prise est plus tardive lorsqu’il fait froid, explique Bruno Paul-Dauphin. Vinci Construction, en lien avec les maîtres d’ouvrage, s’efforce d’intégrer ces contraintes dès la conception des projets en adaptant les types de bétons en fonction des saisons et en développant des équipements spécifiques, comme les banches chauffantes, pour utiliser des bétons très bas carbone même en hiver ».
De même, explique-t-il, les laitiers de hauts-fourneaux bénéficient de propriétés techniques intéressantes notamment en milieu souterrain ou encore en fondation en milieu marin.
Zoom sur les argiles calcinées
Pour pouvoir se substituer au clinker, les argiles sont concassées, séchées, puis activées par passage à 850 °C dans un échangeur thermique cyclonique. Le gain se mesure en partie sur le plan énergétique, car leur température de cuisson est inférieure aux 1 450 °C nécessaires à la production de clinker. Mais l’essentiel du gain est obtenu au niveau des procédés. En effet, la teneur en calcaire des argiles est proche de zéro. Cela limite les émissions de CO2 liées à la réaction chimique de décarbonatation du calcaire responsable de deux tiers des émissions. Ces innovations ont conduit à établir de nouvelles catégories de ciment : le CEM VI, qui intègre des argiles calcinées, et le LC3 (pour « limestone calcinated clay cement ») présenté comme « une solution révolutionnaire ». La formulation du LC3 mise au point à l’École polytechnique de Lausanne remplace en effet la moitié du clinker par de l’argile calcinée et du calcaire broyé. Lafarge a par exemple mis en service une unité de production de ciment bas carbone à partir d’argile locale importée de Bretagne début 2024 sur son site de Saint-Pierre-la-Cour (Mayenne).
Séquestration ou réutilisation du CO2
Ultramédiatisés, les systèmes de capture du carbone arrivent petit à petit à maturité, mais posent trois questions aux acteurs de la filière. Comment financer cet investissement quasi équivalent au prix d’une cimenterie neuve ? Le doublement de la consommation énergétique induit par de tels systèmes est-il soutenable ? Que faire du CO2 capté ? Il faut tout d’abord distinguer la capture du CO2 en vue de sa séquestration dans des stockages géologiques (CCS) de la capture de CO2 en vue de son utilisation (CCUS). Ce gaz peut en effet être mis à profit dans l’industrie cimentière (recarbonatation des bétons déconstruits et des poussières de cimenterie), dans l’agroalimentaire (fabrication de sodas) ou l’industrie chimique en association avec de l’hydrogène pour produire des carburants de substitution pour les transports maritime et aérien.
Quant au stockage géologique, il répond à la volonté européenne de verdir rapidement les industries en enfouissant le CO2 dans des cavités naturelles. Face aux investissements colossaux nécessaires à la décarbonation complète de leur industrie, les cimentiers ne sont-ils pas échaudés par un marché plutôt morose dans la construction neuve ? Laure Hélard reconnaît que « la filière doit composer avec un environnement économique difficile », mais elle invite « à distinguer les éléments liés à la crise conjoncturelle subie par l’ensemble des fabricants de matériaux de construction et la baisse structurelle de la demande dans le bâtiment ».
Cette décroissance est partiellement compensée par des besoins accrus sur les marchés de l’énergie, de l’aménagement, du transport et des mobilités douces. La déléguée générale de France Ciment alerte toutefois sur les risques de « fuite de carbone ». En effet, le clinker, un pondéreux facilement transportable, est notamment exporté par les pays méditerranéens « actuellement en surcapacité ». Une multiplication de ces importations par dix a ainsi été constatée en six ans.
Sur les 19,1 millions de tonnes de ciment consommées en France en 2022, plus de 20 % auraient été fabriquées à partir de clinkers d’importation. « Nous sommes vigilants sur les importations de clinker de pays extraeuropéens qui ne sont pas soumis à un prix du carbone. Les professionnels du secteur attendent la mise en œuvre du mécanisme d’ajustement carbone aux frontières (MACF), un dispositif qui devrait permettre de conserver leur compétitivité », complète-t-elle.
Ce règlement européen entré en vigueur en octobre 2023 devrait être pleinement opérationnel en 2026. Il soumettra le ciment importé dans l’Union européenne à une tarification du carbone équivalente à celle appliquée aux industriels européens. Un levier incontournable pour que la filière se décarbone, tout en restant compétitive.
Les bétons déconstruits, une nouvelle alternative
L’économie circulaire ouvre le champ des possibles grâce aux bétons déconstruits. En France, on compte environ 17 millions de tonnes de granulats de bétons recyclés (GBR) disponibles chaque année. « Plutôt que d’utiliser les GBR en sous-couche routière ou en remblais de carrière, des emplois à faible valeur ajoutée, nous avons développé des procédés capables de séparer les différents constituants initiaux du béton », détaille Alain Cordonnier, président de Fives FCB. Grâce à ces techniques, il est possible de récupérer 50 % de graviers, 30 % de sables et 20 % de ciment hydraté ou « pâte cimentaire ». Cette pâte est susceptible d’être réinjectée dans les procédés d’une cimenterie pour fabriquer du clinker. Le concept a séduit Heidelberg Materials. L’entreprise allemande a démarré début 2024 une première installation industrielle en Pologne permettant de traiter 100 tonnes par heure, pour un investissement de 5 millions d’euros. Une nouvelle norme européenne « Ciment à base de matériaux de construction recyclés » (N F EN 197-6) a par ailleurs été publiée le 7 juin 2023. Seule limite : la disponibilité de la ressource, les bétons étant conçus pour avoir une durée de vie de 70 à 100 ans.
*Le ciment Portland est l’ingrédient de base du béton. Il s’agit d’un liant hydraulique composé principalement de silicates de calcium hydrauliques qui font prise et durcissent en vertu d’une réaction chimique à l’eau appelée hydratation.