SKF utilise l’intelligence artificielle pour faire des économies
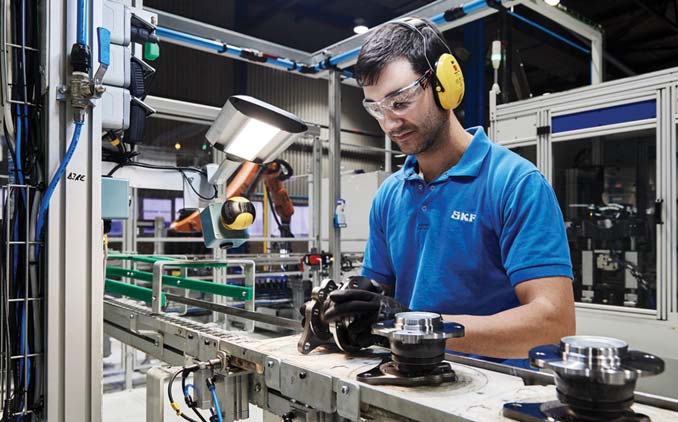
Pour identifier les surconsommations électriques dans leurs usines, les industriels peuvent avoir recours à l’intelligence artificielle. La société Energiency propose des modèles à la carte pour permettre d’identifier les sources de surconsommation et de réaliser des économies d’énergie en menant des actions adéquates. L’industriel suédois SKF a utilisé cette technologie dans son usine de Saint-Cyr-sur-Loire (37).
Si l’intelligence artificielle (IA) est communément associée à la robotique, elle peut aussi aider les sur l’apprentissage automatique à faire des économies d’énergie. Le concept d’IA, au croisement entre l’informatique, les mathématiques et l’analyse des des données, émerge dans les années 50. Mais il faudra attendre les progrès des ordinateurs avant que le concept ait des applications concrètes. C’est au cours des années 90 que l’IA a réellement franchi un cap : en 1997, un ordinateur, le DeepBlue d’IBM bat pour la première fois Gary Kasparov, le meilleur joueur d’échecs du monde de l’époque. Concrètement, une IA est un programme informatique capable d’ajuster ses comportements en fonction des traitements qu’il doit effectuer. L’entreprise Energiency a mis au point un programme permettant d’identifier des gisements d’économie d’énergie à partir des données fournies par les industriels.
Deux familles de modèles
La société utilise deux familles de modèles. La première repose sur l’apprentissage automatique (machine learning) et se fonde sur des approches mathématiques et statistiques pour donner aux ordinateurs la capacité d’apprendre à partir de données. La seconde est liée aux réseaux de neurones artificiels, qui fournissent à l’IA un mécanisme perceptif indépendant des idées propres de l’implémenteur. Pour utiliser ces modèles, Energiency part donc des données fournies par les industriels (consommations d’énergie, types de fluides utilisés dans l’usine, cadences des chaines de production, matériels construits, météorologie, etc). Une fois ces paramètres récupérés, il faut dans un premier temps les nettoyer afin de construire un jeu de données pertinent, puis exercer le modèle et mesurer ses performances.
Une étude du potentiel de gain d’énergie par rapport aux données antérieures est également réalisée. « Nos modèles sont ensuite implémentés sur la plateforme de l'industriel Ils nous alertent lorsque des phénomènes de surconsommation sont détectés, tout en nous permettant d’identifier les facteurs à l’origine des écarts », explique Thierry d’Allance, directeur commercial chez Energiency. Enfin, la société fournit à ses clients un bilan annuel des économies réalisées et procède à des mises à jour régulières des modèles, en général une fois par an, dans une logique d’amélioration continue.
SFK et l’initiative “Beyond Zero”
Pour réduire ses consommations, une usine appartenant à l’industriel suédois SFK, implantée à Saint-Cyr-sur-Loire (37) a fait appel aux modèles développés par Energiency. Le site fabrique des roulements pour 40 filières, principalement pour le secteur automobile et dans une moindre mesure, pour le ferroviaire.60 millions de roulements sortent de l’usine chaque année. Pour SKF qui gère huit sites de production en France, économiser de l’énergie n’est pas une idée nouvelle. Dès 2006, il lançait une initiative baptisée “Beyond Zero”. L’objectif ? Générer des économies sans forcément changer le matériel des chaines de production. « Nous avons essayé de ne pas utiliser d’énergie hors production, ni consommer plus d’énergie que le besoin réel. Nous avons utilisé ces préceptes sur les centrales fluides de coupe, sur l’air comprimé, en installant notamment des variateurs de vitesse », rapporte Bruno Valenti, responsable assistance technique et coordination chez SKF France. Les résultats ont été concluants. Entre 2006 et 2016, la consommation électrique sur la centrale des fluides a baissé de 34 % et celle générée par l’air comprimé de 17 %. « À ce moment-là, nous avons atteint un palier. Il fallait trouver d’autres outils pour aller plus loin », poursuit Bruno Valenti. D’autant plus que la direction du groupe a déjà défini de nouveaux objectifs climatiques particulièrement élevés. D’ici 2025, SKF envisage de baisser de 40 % les rejets de CO2 par tonne de roulements vendus et par tonne de produits expédiés par rapport à 2015. Cinq ans plus tard, les usines devront devenir neutres en carbone.
Des résultats rapides...
SKF a donc décidé de collaborer avec Energiency pour poursuivre ses économies d’énergie. L’usine de Saint-Cyr-sur-Loire consommait 45 877 MWh pour une facture de 3,3 millions d’euros en 2019. Les deux entreprises ont collaboré sur un bâtiment qui fabrique 10 000 roulements chaque année. « Deux modèles d’IA ont été mis en place pour l’électricité et l’air comprimé. Pour le créer, nous avons fourni 18 mois de données », détaille le responsable assistance technique et coordination. À partir de ces éléments fournis par quelques compteurs seulement, Energiency a dégagé un potentiel de gain de 3,5 % d’électricité. Puis, l’entreprise a déployé une application, dotée d’indicateurs de performance affichés sur un tableau de bord, pour alerter en temps réel l’industriel d’éventuelles surconsommations. Lorsque la consommation est dans le vert, c’est que tout est normal. L’orange représente une consommation excessive inférieure à 10 % et le rouge une consommation supérieure de 10 % aux prévisions. Cela a permis de détecter certaines anomalies et déployer des actions concrètes.
... et meilleurs que ceux attendus
« Concernant l’air comprimé, nous évitons de travailler à de fortes pressions si des pressions plus faibles suffisent », souligne Bruno Valenti. SKF a aussi zoné les ateliers avec des vannes et des débitmètres. Quand un technicien quitte son poste, l’air est coupé. En effet, 32% de l’électricité était consommée hors production. Aujourd’hui, ce chiffre est tombé à 11%. Le site coupe aussi l’aspiration quand la production est à l’arrêt. Pour automatiser ce process, SFK a couplé les machines dédiées à la production d’air à celles chargées de l’aspiration. Le résultat : une réduction de la facture de 10000 euros pour seulement 1 500 € d’investissement. Enfin, les distributeurs d’air comprimé ont été remplacés. « Nous utilisions des distributeurs qui fonctionnaient à six bars minimums. Aujourd’hui, ils ont été remplacés par des appareils qui se contentent d’une pression de 4,2 et permettent de réduire les consommations d’air de 32 % en fonctionnement », indique Bruno Valenti. Grâce à l’apport de l’IA et à toutes les actions entreprises, l’usine a réduit sa demande d’électricité de 6 % alors que les modèles développés par Energiency tablaient au départ sur un chiffre de 3,5 %. Le groupe scandinave n’a pas eu à réaliser des dépenses très importantes pour atteindre ce résultat. Le retour sur investissement s’est fait en un an seulement. Malgré ces bons résultats, les deux partenaires tentent d’améliorer encore les modèles, en particulier celui consacré à l’air comprimé. En effet, elles ont constaté au bout de deux ans de fonctionnement qu’elles ne recevaient plus d’alarmes. « Nous avons donc recalculé le modèle avec les données de référence de 2019. Nous avons constaté des dérives que nous allons essayer de régler pour économiser encore quelques pourcents d’énergie supplémentaires », conclut Bruno Valenti.