Brasserie Goudale : moins de consommation, plus de production
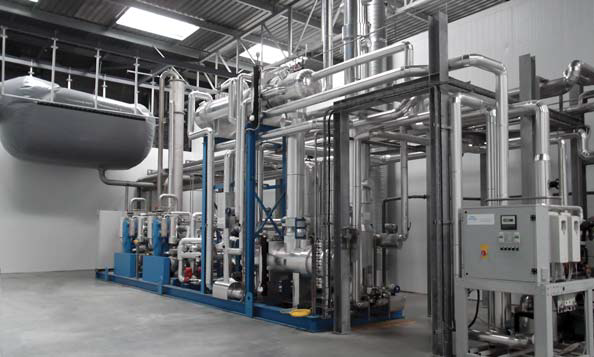
En 2016, la Brasserie Goudale a déménagé à Arques (62) dans une nouvelle usine, permettant au groupe de considérablement augmenter sa production et de réduire ses impacts environnementaux. Une attention particulière a été portée sur la production de froid. C’est Axima Réfrigération, filiale d’Engie Solutions, qui s’est chargée d’installer ces équipements.
Après un siècle d’existence, la Brasserie Goudale s’est installée dans une nouvelle usine en septembre 2016. Les deux phases de travaux ont nécessité pour l’entreprise un investissement total de 125 millions d’euros. Nouvelle vitrine du groupe, le site implanté à Arques (62) a été construit pour augmenter la production de bière. Dès sa première année de service, un million d’hectolitres est brassé sur place. En 2018, une nouvelle salle de brassage et un bâtiment de stockage de près de 25000 m² sont ajoutés dans le but de doubler la capacité de la brasserie qui s’élève aujourd’hui à 2,5 millions d’hectolitres.
Malgré cette hausse de production spectaculaire, elle consomme trois fois moins d’eau par litre de bière produit et deux fois moins d’énergie (en valeur absolue) que l’ancienne brasserie implantée à Douai. Pour parvenir à ce résultat, le groupe a fait installer des groupes frigorifiques plus efficaces. « Sur une usine de ce type, la partie de production de froid représente entre 50 et 60 % de la consommation électrique », souligne Julien Dupré, responsable efficacité énergétique et environnementale chez Axima Réfrigération, filiale d’Engie Solutions qui s’est occupée de l’installation et du suivi de ces équipements. Un système destiné à récupérer de la chaleur fatale a aussi été mis en place.
Optimisation du process
Les travaux ont été menés en deux phases. « La première livraison a été faite en septembre 2016. C’est une installation frigorifique de 2,4 MW pour générer de l’eau glycolée à -6 °C », détaille Julien Dupré. En guise de fluide frigorigène, l’installation utilise de l’ammoniac (NH3), un des fluides les plus économes en énergie, qui n’est pas un gaz à effet de serre (GES) et ne dégrade pas la couche d’ozone. Il coûte aussi moins cher que les hydrofluorocarbures (HFC). L’installation intègre une régulation par haute pression flottante qui permet de gérer la pression de condensation. Celle-ci maintient une température de condensation plus basse en fonction de la température extérieure, ce qui réduit le temps de fonctionnement, l’intensité absorbée par les ventilateurs et les compresseurs, tout en augmentant le coefficient de performance de l’installation.
Des variateurs de vitesse ont aussi été montés sur les compresseurs, les pompes et les moteurs des condenseurs. « En 2018, lorsque la brasserie s’est étendue, nous avons ajouté 4,9 MW de froid supplémentaire », relate Julien Dupré. Si elle est deux fois plus puissante, la nouvelle unité repose pourtant sur les mêmes technologies (HP flottante, NH3, variateurs de vitesse). Toutefois, elle est équipée d’un système de récupération de chaleur fatale de 800 kW destiné à alimenter en chauffage le hall du bâtiment.
Récupération de CO2
En 2019, un système de récupération, de purification et de liquéfaction de CO2 est venu compléter l’ensemble. Lors de la phase de fermentation de la bière, du CO2 est dégagé. N’étant pas assez pur pour être réutilisé directement dans un cadre alimentaire, le CO2 a besoin d’être traité. Après avoir été capté, il est donc purifié dans des colonnes et séché pour atteindre une pureté supérieure à 99,99 %, soit la qualité alimentaire requise pour le réutiliser. Ensuite, le CO2 est liquéfié, puis vaporisé. Il sert alors à créer les bulles et la mousse de la bière lors d’une étape appelée carbonatation forcée. Ce système peut récupérer une tonne de CO2 liquide par heure et en vaporiser deux tonnes. La brasserie est donc autonome en CO2 et n’importe plus de gaz en bouteille.